Wendy’s is where food is made fresh—never frozen. But no matter how fresh your kitchen’s ingredients may be, its equipment must be working properly in order to really deliver that brand promise.
Wendy’s franchisees partner with 86 Repairs to ensure that can happen. We handle the repair and maintenance (R&M) process from end to end for common kitchen equipment so staff can keep their focus on customers.
Part of that process includes basic troubleshooting. Before spending the time and money on vendor dispatch, we walk staff through simple solutions to common issues. It helps reduce downtime—and the number of unnecessary invoices for R&M.
We spoke to Wendy’s franchise owners and operators to understand which equipment gives them the most issues. From our conversations, we’ve identified troubleshooting tips for Frosty machines, lemonade bubblers, and grills that can help your business avoid extra repair expenses.
These are general tips. Wendy’s teams should always defer to the troubleshooting steps and advice found in the user manuals for the specific make and model of units found in their kitchens. And remember: when in doubt, an internal tech or authorized external vendor will be able to help.
Table of Contents
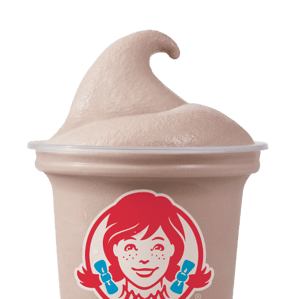
Frosty machine troubleshooting
Frostys are an iconic dessert—and the only place they’re found is Wendy’s. So when the Frosty machine is on the fritz, it’s extremely important to get it back up and running so customers can get the cold treat they crave.
Unit not working
There could be a few reasons why the Frosty machine won’t dispense its delicious treat:
- Is the unit unplugged? If so, plug it back into a working outlet.
- Is the outlet working? Check that it has power.
- If it doesn’t have power, reset the circuit using these directions.
- Is there mix in the hopper? Make sure it’s filled to the right place.
- Is the beater motor working? If not, reset the freezer to try and turn it back on.
No Frosty dispensing
Before troubleshooting, be sure your unit is in “Auto” mode and the draw valve is open. If Frostys still won’t dispense,
- Verify the outlet the unit is plugged into has power. If it doesn’t reset the circuit using these directions.
- There could be a problem with the beater motor. Reset the freezer to try and turn it back on.
- You might not have enough mix in the hopper. Be sure to fill it to the right place so Frostys can freeze and be dispensed.
If those troubleshooting steps don’t work, the machine could have a freeze in the mix inlet hole, or the beater could be rotating in the wrong direction. Call an authorized technician to take a closer look.
Wrong consistency
Frostys have a very specific look and feel—thicker than a milkshake, but not solid soft-serve.
If the Frosty consistency is too stiff,
- Check the mix. Is there enough in the hopper? If not, fill it to the right level.
- Check the thermistor. Is it too cold? If so, contact an authorized vendor to adjust.
If the Frosty consistency is too soft,
- Check the condenser. Is it dirty, or is there enough space around it to promote airflow? Remember to remove debris from the condenser monthly and keep the unit in a place where air can flow freely into and out of the condenser.
- Check the scraper blades. Are they too worn? If so, replace them.
- Check the mix. Was it left over from yesterday? Only fresh mix should be used for an optimal product.
- Check the thermistor. Is it too warm? If so, contact an authorized vendor to adjust.
Unit leaking
If the unit is leaking into the drive shaft drip pan,
- Check the drive shaft seal. Is it missing, worn, or improperly installed? If so, replace or reinstall.
- Check the lubrication of the drive shaft. Make sure it’s been lubricated in accordance with manufacturer directions.
- Check the rear shell bearing. If it’s worn, an authorized vendor will need to be called in for replacement.
If the unit is peaking from the door spout,
- Check the o-rings on the valve. Are they missing or worn? If so, replace.
- Check the lubrication of the o-rings. Are they lubed according to manufacturer directions, including the proper kind of lubricant? If not, lubricate properly.
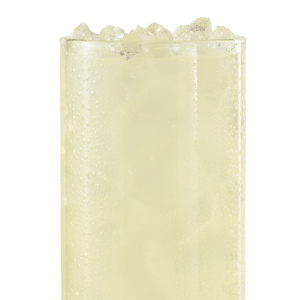
Lemonade bubbler troubleshooting
Fruit puree, juice, and the water added to balance out the recipe need to be agitated to avoid one flavor coming through the machine too strongly. Enter: the bubbler. These machines keep liquid mixtures—like Wendy’s lemonades—constantly moving so the recipe is always right.
If the bubbler is being a bother, try these troubleshooting tips.
No refrigeration
Lemonade mixture not getting cold? There are a few things to check:
Is the compressor running? If not, you’ll need to call a technician right away.
But if the compressor is running,
- Check the condenser. Is it clogged with dust and debris? If so, unplug the unit and clean out all lint and dust from inside. A vacuum cleaner or bottle brush can make this process quicker.
- Check the motor. Is it working? If not, the motor may need to be replaced. Call for service.
- Check the refrigerant. Is it at the correct level? If not, there may be a leak. Call for service with this issue, too.
No spray or agitation
Let’s try to give the lack of mixing a quick fixin’:
If the unit won’t spray, but the motor is running, check the impeller.
- Is the impeller itself or its sleeve too worn? If so, replace them. If not, clean them thoroughly. The impeller has to spin freely on its sleeve to spray—and refrigerate—properly.
- Is the impeller rattling? If so, it’s probably not spinning how it should. Increase the height of the drive magnet on the motor shaft, but not too high that it rubs against the surface. Check the user manual for precise advice on how to do this.
If there’s no spray and the motor is not running, you’ll need to call a vendor.
Unit leaking
There are two common places where a bubbler can leak: from the bowl and from the valve.
- Bowl leaks are usually caused by gasket issues. They could be worn, nicked, or improperly installed. To fix the leak, check the user manual for bowl assembly and reinstall the gasket. If the gasket is worn or damaged, replace it.
- Valve leaks are usually caused by buildup or issues with the o-ring. To fix the leak, remove and clean both the valve and o-ring in accordance with the user manual. If the o-ring is worn or damaged, replace it.
Unit making unusual sounds
There are two common culprits for this issue, too: fan blades and bearings.
- Check the fan blades. If they’re bent, unplug the unit and bend the blade back into place for proper alignment.
- Check the bearings in both the fan and spray motors. If they’re worn, a vendor will be needed for replacement.
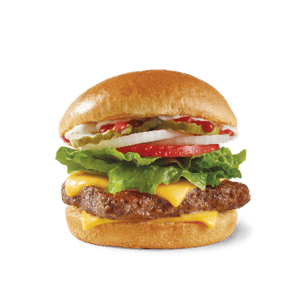
Grill troubleshooting
You can’t serve famous square burgers if they aren’t cooked correctly. When the heat is on to get a grill fixed fast, try these ideas.
Note: We’ve heard from Wendy’s operators that their grills may be much more complicated than what these standard troubleshooting tips may suggest. For Wendy’s grills, it’s even more important to follow manufacturer troubleshooting instructions to a T.
No power
Verify that the hood system is working.
- If it’s not, it’s probably affecting the power flow to the unit. Troubleshoot hood problems here.
Check to see if the grill is correctly connected to a power source.
- For gas grills, ensure the gas supply is turned on and no gas leaks are present.
- For electric grills, ensure the power cord is securely plugged into the unit and an outlet.
If an electric grill is plugged in and not turning on, there could be a problem with the electrical current and not the unit itself.
- Plug the grill into another outlet to see if it receives power.
- If there’s still no power, try toggling the breaker for the general area where the grill is plugged in.
- If toggling the breaker doesn’t work, the GFI may have tripped. Hit the “Test/Reset” buttons on the outlet.
Not heating
This is likely a pilot light or cleaning issue.
- Verify the pilot is still lit. Look for a flame through the holes next to the burner knobs.
- If the pilot is out, relight it. Be sure to wait between attempts so your safety failsafe doesn’t shut the gas to the pilot.
- If the pilot is on, clean the grill burners. Remove buildup with scouring pads.
Call a vendor to investigate further if troubleshooting doesn’t give your grill heat or power.
Uneven cook
Is the grill getting cleaned regularly? Built-up grease and residue can cause uneven heating, potential flare-ups, and other grill issues.
Make regular grill cleaning a habit, including the burners, ignition, grates, and drip trays! Correct and consistent maintenance like this can prevent many common grill issues.
Take repairs off your plate
R&M taking too much of your team’s time? We can help. Wendy’s franchisees get 24/7 on-demand support from real people with restaurant experience so owners and operators can have peace of mind that repairs are getting done—and managers get fewer frantic calls when they’re off the clock.
We don’t just help frontline staff, though. We support internal technicians, too! Every service request and ticket is stored in one convenient place so they get complete visibility into the status of every repair across every location while they’re dealing with bigger priorities.
Click the “Learn More” button at the top of the page to see how our solution can support your growing business.